Injection Molding Automotive: A Comprehensive Guide
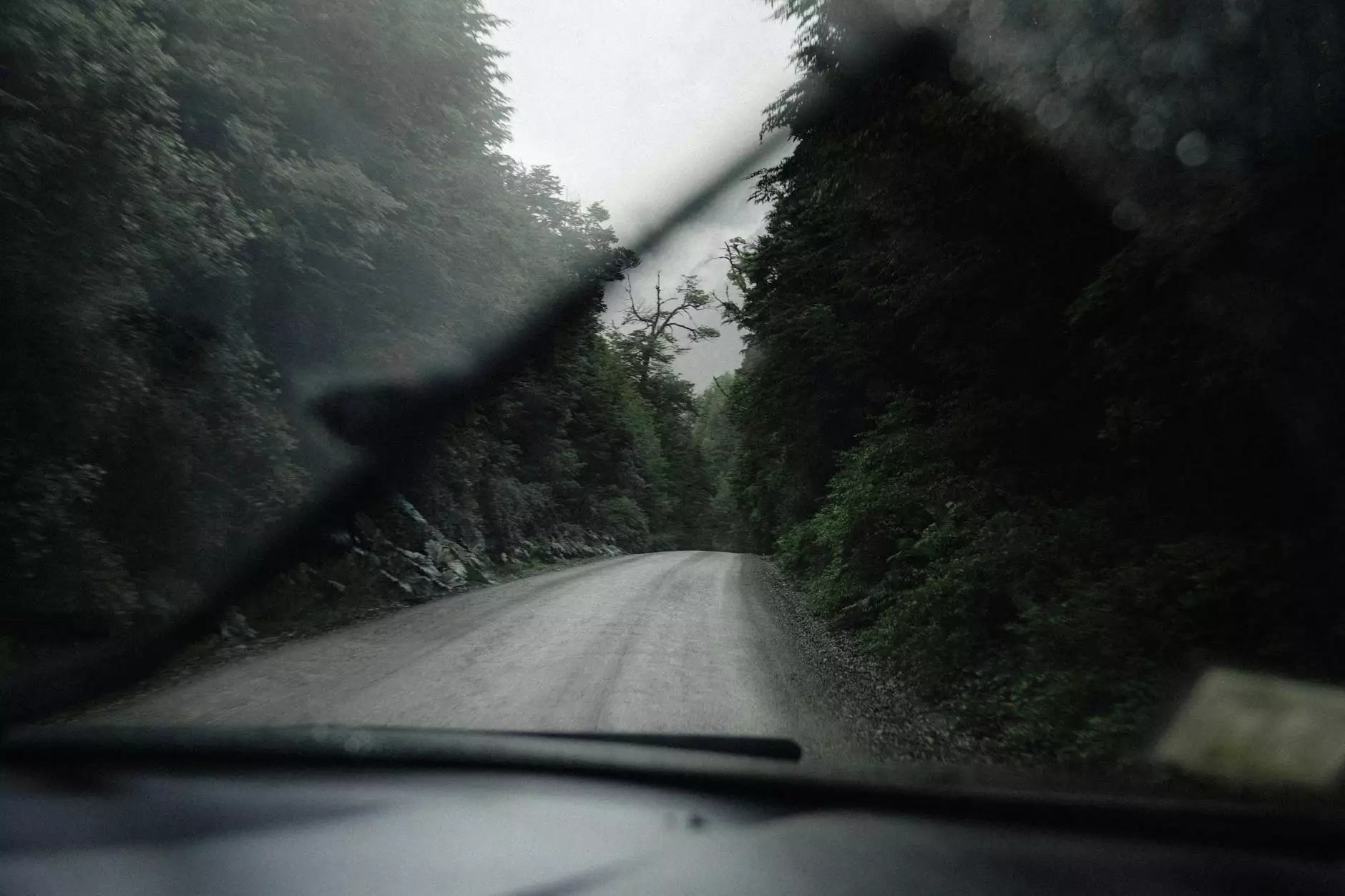
In the ever-evolving world of the automotive industry, the demand for innovative manufacturing techniques has never been higher. Among these techniques, injection molding has emerged as a crucial process, particularly when it comes to producing high-quality parts that meet rigorous standards. In this article, we dive deep into the realm of injection molding automotive and explore its significance, advantages, methodology, applications, and the future it holds within the automotive landscape.
Understanding Injection Molding
Injection molding is a versatile manufacturing process that involves injecting molten plastic into a mold to create a specific shape. This process has gained immense popularity in various industries, particularly in automotive manufacturing, due to its ability to produce complex parts with high precision.
How Does Injection Molding Work?
- Material Selection: The process begins with selecting the appropriate thermoplastic material, which is usually based on the required strength, flexibility, and appearance of the final product.
- Mold Design: A precisely engineered mold is designed to create the desired shape of the part to be produced. This is a critical step that dictates the efficiency and quality of production.
- Heating and Injection: The selected material is heated until it becomes molten and is then injected into the mold cavity at high pressure.
- Cooling: The molten material is allowed to cool and harden within the mold, taking the shape of the cavity.
- Demolding: Once cooled, the mold is opened, and the newly formed part is ejected.
This process can produce thousands of identical parts with minimal waste, which makes it highly efficient.
Advantages of Injection Molding in the Automotive Sector
The automotive industry benefits greatly from the application of injection molding. Here are some of the key advantages:
- Cost-Effectiveness: While the initial investment in molds can be high, the cost per part significantly decreases with mass production, making it economically viable.
- Precision and Consistency: Injection molding provides unparalleled accuracy, ensuring that each part meets strict specifications, crucial for safety and performance in vehicles.
- Material Versatility: A wide range of thermoplastics can be used, including ABS, polypropylene, and polycarbonate, allowing for the production of various components.
- Complex Designs: The process enables the creation of intricate shapes and detailed features that are often difficult or impossible to achieve with other manufacturing methods.
- Reducing Waste: Because the process uses only the necessary amount of material to create each part, waste is minimized, making it an environmentally friendly option.
Applications of Injection Molding in Automotive Manufacturing
Injection molding is used to manufacture a wide array of automotive components. Common applications include:
- Interior Components: Parts such as dashboards, panels, and trims, which require aesthetic appeal and durability.
- Exterior Parts: Bumpers, grilles, and body panels, which must withstand environmental factors.
- Functional Components: Items such as clips, fasteners, and connectors that play vital roles in vehicle assembly.
- Electrical Housings: Protective enclosures for wiring and electronic components which must provide insulation and protection from interference.
Case Studies in Automotive Injection Molding
Let's take a look at some prominent examples where injection molding automotive applications have been successfully implemented:
Case Study 1: Automobile Dashboard Production
A major automobile manufacturer sought to reduce the production cost of its dashboard assembly. By utilizing injection molding for the dashboard components, the company achieved:
- Reduced material costs through efficient use of plastics.
- Increased production speed, allowing for a higher output.
- Improved design flexibility, enabling the introduction of new features without a significant overhaul of production processes.
Case Study 2: Bumper Production
Another example involves the production of vehicle bumpers, which traditionally relied on metal fabrication. The switch to injection molding resulted in:
- Weight reduction, which is crucial for fuel efficiency.
- Enhanced impact resistance thanks to modern polymer formulations.
- Significantly lower production costs by streamlining the manufacturing process.
The Future of Injection Molding in Automotive
The future of injection molding automotive is poised for significant advancements driven by technological innovations and changing industry demands. Key trends include:
1. Advanced Materials
The development of new and advanced materials, such as lightweight composites and bioplastics, will expand the capabilities of injection molding. These materials will allow manufacturers to produce more sustainable and environmentally friendly components.
2. 3D Printing Integration
As 3D printing technology evolves, its integration with traditional injection molding processes can lead to the rapid prototyping of molds. This hybrid approach can enhance design capabilities and reduce time-to-market for new automotive parts.
3. Automation and Smart Manufacturing
The rise of automation and smart manufacturing technologies will streamline the injection molding process, resulting in higher efficiency, reduced costs, and minimized human errors.
4. Focus on Sustainability
With a growing emphasis on sustainability, the automotive industry is shifting towards more environmentally friendly manufacturing processes. Injection molding manufacturers are investing in techniques that reduce energy consumption and waste.
The Role of Metal Fabricators in Injection Molding
While injection molding primarily uses plastics, metal fabricators play an essential role in the automotive supply chain. They are responsible for creating the molds used in injection molding processes. Here's how they contribute:
- Mold Production: Metal fabricators design and manufacture high-precision molds that dictate the quality and intricacy of the injection-molded parts.
- Maintenance and Repair: They ensure that molds are well-maintained and repaired, which is critical for consistent production quality.
- Collaboration: Metal fabricators often work closely with automotive engineers to optimize mold designs for both performance and cost.
Conclusion
In summary, injection molding automotive is a pivotal process that enables the production of high-quality, precise components essential for modern vehicles. Given its numerous advantages, diverse applications, and the promising future driven by technological advancements, it is clear that injection molding will continue to be a cornerstone of the automotive manufacturing landscape. As manufacturers and metal fabricators alike innovate and collaborate, the industry will keep pushing the envelope for efficiency, sustainability, and performance in automotive production, paving the way for a new era of vehicle manufacturing.
For more information about injection molding and related services, visit deepmould.net.