Understanding Injection Mold Tooling
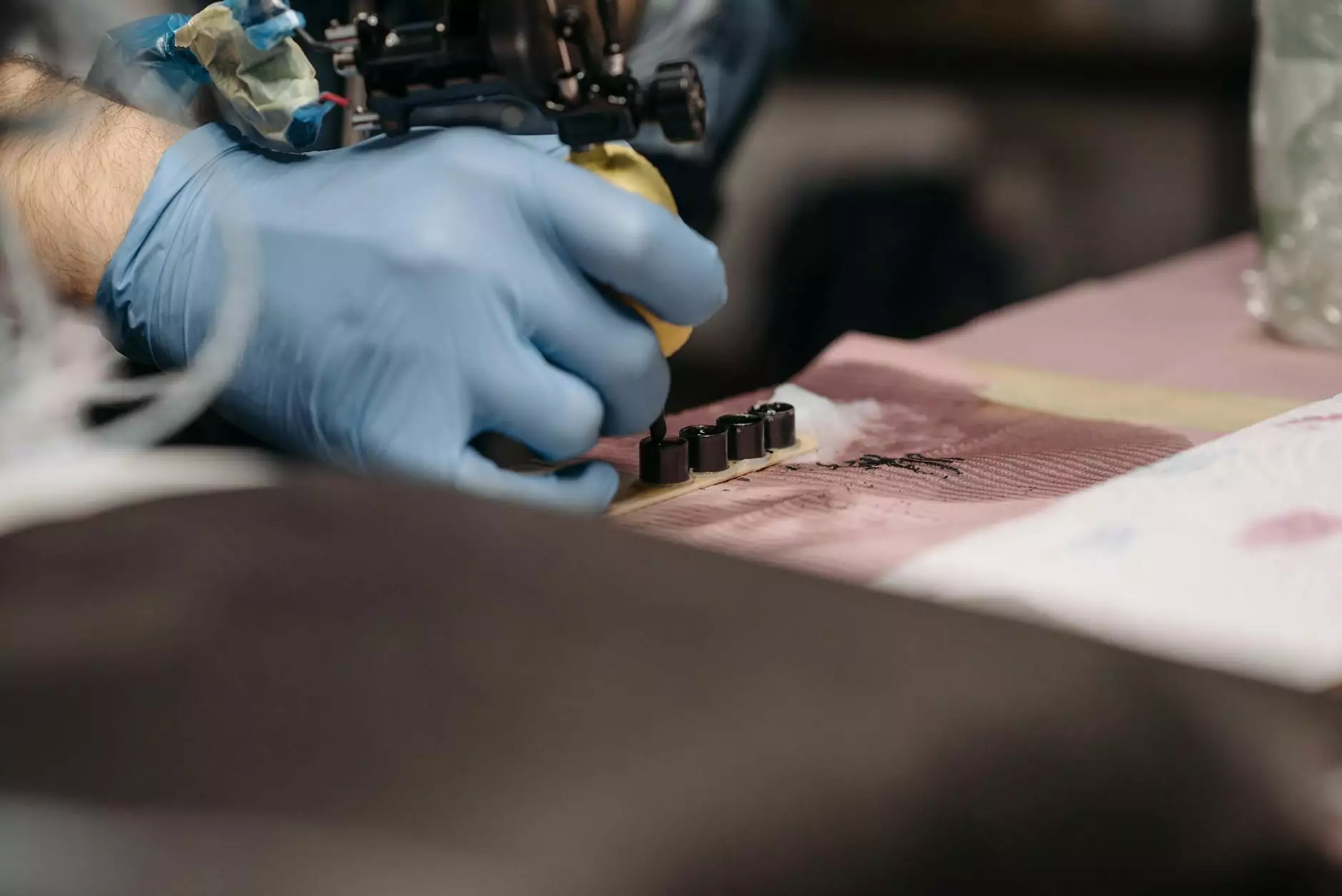
Injection mold tooling is a critical aspect of the manufacturing process, particularly in the world of metal fabrication. It serves as the foundation for producing high-quality, precise parts consistently. This article delves deep into the nuances of injection mold tooling, discussing its significance, applications, and what makes it an essential component in the industry.
What is Injection Mold Tooling?
Injection mold tooling refers to the process of creating a mold into which molten material is injected to form a specific shape. In metal fabrication, this often involves the use of thermoplastics or other metals that are heated until they become pliable. Once injected into the mold, the material cools and solidifies, creating the desired part with exceptional accuracy.
Why is Injection Mold Tooling Important?
The importance of injection mold tooling in manufacturing cannot be overstated. Here are several reasons why it stands out:
- Precision: Molds are designed to provide precise dimensions, ensuring that every part produced meets the specifications closely.
- Cost-Effectiveness: Although the initial investment in mold creation can be significant, it pays off through reduced production costs over time, especially for high-volume production.
- Consistency: Injection molds produce consistent parts with minimal deviation, which is crucial for industries where quality assurance is paramount.
- Complex Geometries: Injection molding allows for the creation of complex shapes that may be challenging to achieve with other manufacturing processes.
- Material Versatility: Various materials can be used in injection molding, including metals, plastics, and elastomers, making it a versatile option for manufacturers.
Key Components of Injection Mold Tooling
Understanding the components involved in injection mold tooling helps grasp its functionality. The essential components include:
1. Core and Cavity
The mold is generally made up of two halves - the core and the cavity. The core is the interior part that shapes the inner contour of the piece, while the cavity shapes the outer contour.
2. Ejector Pins
Ejector pins are vital for removing the finished part from the mold. They push the cooled piece out of the mold once it has solidified.
3. Cooling System
A sophisticated cooling system is integrated to manage the temperature of the mold, ensuring that the material cools evenly and reduces cycle times.
4. Guide Pins
Guide pins ensure accurate alignment of the mold halves during closure, which is crucial for maintaining the integrity of the part shape.
The Injection Molding Process
The process of injection mold tooling can be broken down into several stages:
- Material Preparation: The chosen material is prepared, often requiring preheating or drying for optimal flow characteristics.
- Injection: The molten material is injected into the mold under high pressure to fill the cavity completely.
- Cooling: The material cools and solidifies within the mold, taking the shape of the cavity.
- Ejection: Once cooled, the ejector pins push the solid part out of the mold.
- Trimming and Finishing: Any excess material (flash) is trimmed away, and finishing processes can be applied if required.
Applications of Injection Mold Tooling in Metal Fabrication
Injection mold tooling is used across various industries, demonstrating its versatility and efficiency. Here are some notable applications:
1. Automotive Industry
The automotive sector extensively uses injection molding for creating complex components like dashboards, interior trims, and housings for lights and controls.
2. Consumer Electronics
Modern electronics often rely on injection-molded parts due to their precision and ability to accommodate intricate designs. Components such as casings for smartphones and laptops are typical examples.
3. Medical Devices
The medical industry demands high-quality components, and injection mold tooling is capable of meeting stringent regulatory standards while delivering precision parts, from syringes to surgical instruments.
4. Household Goods
Everyday items, such as containers, toys, and appliances, benefit from injection-molded parts, underscoring the process's role in mass consumer goods production.
Advantages of Choosing DeepMould for Injection Mold Tooling
When it comes to injection mold tooling, selecting the right partner is essential. DeepMould stands out in the metal fabrication landscape for several reasons:
- Expertise: DeepMould boasts a team of seasoned professionals with extensive knowledge in mold design and manufacturing.
- Advanced Technology: Using state-of-the-art technology and machinery ensures high-quality output and efficiency.
- Customization: Each project is tailored to meet specific client needs, ensuring that the final product aligns with the exact requirements.
- Quality Assurance: Adherence to stringent quality checks ensures that every piece produced meets industry standards.
- Timely Delivery: DeepMould prides itself on adhering to deadlines, ensuring that production timelines are met without sacrificing quality.
Challenges in Injection Mold Tooling
Like any manufacturing process, injection mold tooling does come with its challenges. Understanding these can provide deeper insights into the process:
1. High Initial Costs
One of the most significant barriers to using injection molding is the high initial cost associated with creating custom molds, which can deter small businesses.
2. Design Constraints
While injection molding can create complex shapes, certain design constraints must be observed to ensure the mold functions well and parts are ejected successfully.
3. Material Limitations
Not all materials are suitable for injection molding, and selecting the wrong type could lead to suboptimal results or manufacturing issues.
Future Trends in Injection Mold Tooling
The future of injection mold tooling is promising, with advancements making the process more efficient and effective. Here are some trends to watch:
- Industry 4.0: The integration of smart technology, data analytics, and IoT is expected to optimize the injection molding process.
- Sustainability: Increased focus on using eco-friendly materials and sustainable practices is shaping the future landscape of mold tooling.
- 3D Printing Integration: The hybrid approach of combining traditional molding with 3D printing for prototype development is gaining traction.
- Lightweight Materials: The demand for lightweight products, particularly in automotive and aerospace applications, is driving innovation in material science.
Conclusion
In summary, injection mold tooling is a cornerstone of modern manufacturing, particularly within metal fabrication. The precision, efficiency, and versatility it offers make it ideal for numerous applications. Collaborating with industry experts like DeepMould can enhance product quality and manufacturing efficiency, ensuring that businesses remain competitive in a dynamic marketplace. As technology advances, the potential for injection molding only continues to grow, paving the way for innovations that will shape the future of manufacturing.